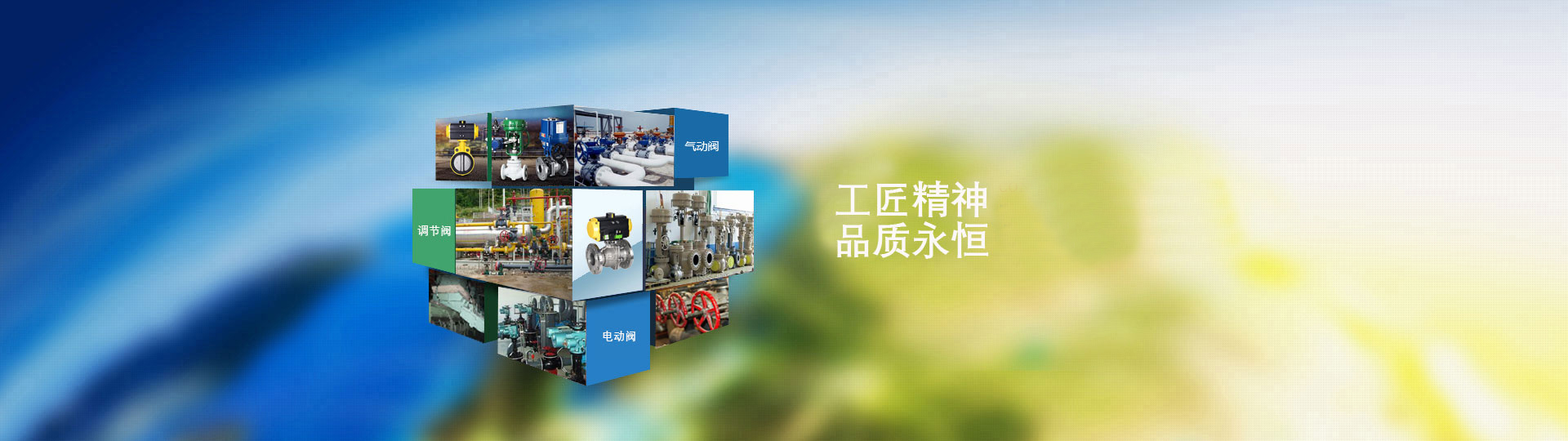
閥門鑄造工藝方法及常見缺陷防治方法更新日期:2021-04-01
閥體的鑄造是閥門制造過程的重要環(huán)節(jié),閥門鑄件質(zhì)量的好壞就決定了閥門質(zhì)量的好壞。下面介紹閥門行業(yè)常用的幾種鑄造工藝方法:
砂型鑄造:
閥門行業(yè)常用的砂型鑄造,按粘結(jié)劑的不同還可分為:濕型砂、干型砂、水玻璃砂和呋喃樹脂自硬砂等。
(1) 濕型砂是以膨潤(rùn)土為粘結(jié)劑的造型工藝方法。
它的特點(diǎn)是:造好的砂型不需要烘干,不需要經(jīng)過硬化處理,砂型有一定的濕態(tài)強(qiáng)度,砂芯、型殼的退讓性較好,便于鑄件的清理落砂。造型生產(chǎn)效率高,生產(chǎn)周期短,材料成本低,便于組織流水線生產(chǎn)。
它的缺點(diǎn)是:鑄件易產(chǎn)生氣孔、夾砂、粘砂等缺陷,鑄件的質(zhì)量尤其是內(nèi)在質(zhì)量不夠理想。
鑄鋼件濕型砂的配比及性能表:
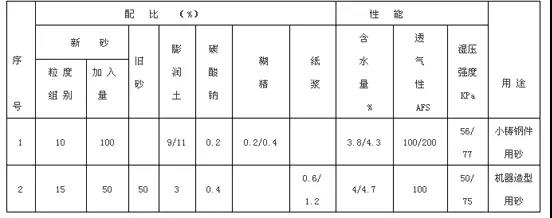
它的缺點(diǎn)是:需要砂型烘干設(shè)備,生產(chǎn)的周期較長(zhǎng)。
(3)水玻璃砂是以水玻璃為粘結(jié)劑的造型工藝方法,它的特點(diǎn)是:水玻璃遇CO2后有自動(dòng)硬化的功能,可有氣硬化法造型和造芯的各種***點(diǎn),但存在型殼潰散性差,鑄件清砂困難以及舊砂再生、回用率低的缺點(diǎn)。
水玻璃CO2硬化砂配比及性能表:
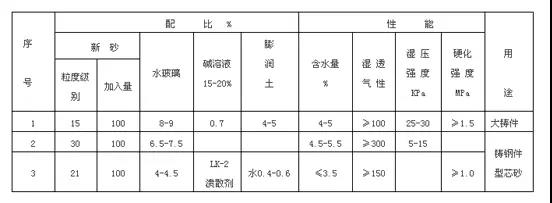
呋喃樹脂自硬砂混合料配比及混制工藝:

混制樹脂砂時(shí)各種原料的加入順序如下:
原砂+固化劑(對(duì)甲苯磺酸水溶液)-(120~180S)-樹脂+硅烷-(60~90S)-出砂
(5)典型的砂型鑄造生產(chǎn)流程:
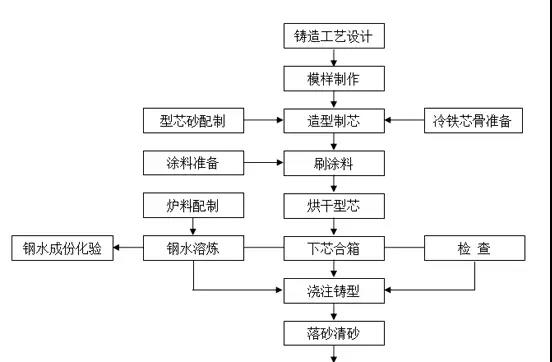
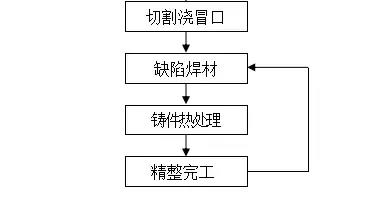
近年來,閥門廠家越來越注重鑄件的外觀質(zhì)量和尺寸精度。因?yàn)榱己玫耐庥^是市場(chǎng)的基本要求,也是作為機(jī)加工頭道工序的定位基準(zhǔn)。
閥門行業(yè)常用的精密鑄造是溶模鑄造,現(xiàn)簡(jiǎn)要介紹如下:
(1)溶模鑄造的兩種工藝方法:
①采用低溫蠟基模料(硬脂酸+石蠟)、低壓注蠟、水玻璃型殼、熱水脫蠟、大氣熔煉澆注工藝,主要用于質(zhì)量要求一般的碳素鋼和低合金鋼鑄件,鑄件尺寸精度可達(dá)標(biāo)準(zhǔn)CT7~9級(jí)。
②采用中溫樹脂基模料、高壓注蠟、硅溶膠模殼、蒸汽脫蠟、快速大氣或真空熔煉澆注工藝,鑄件尺寸精度可達(dá)CT4~6級(jí)的精密鑄件。
(2)溶模鑄造典型工藝流程:
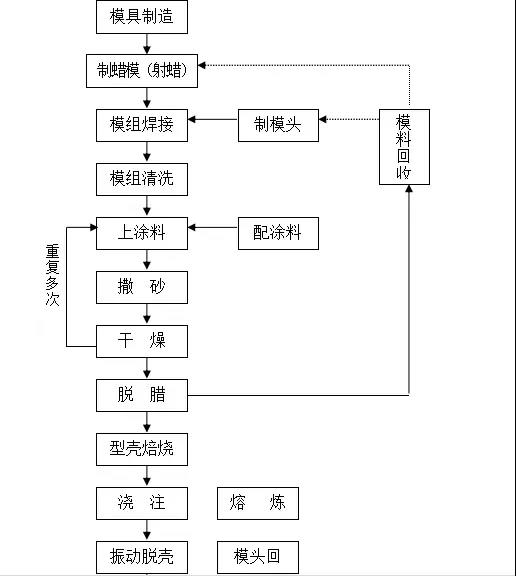
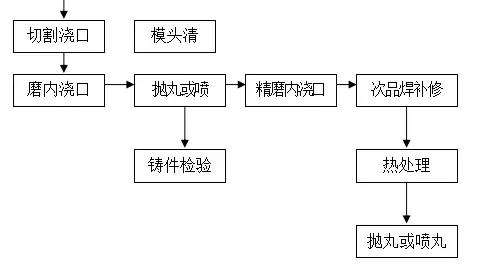
①鑄件尺寸精度高,表面光整、外觀質(zhì)量好。
②可以鑄造結(jié)構(gòu)形狀復(fù)雜、難以用其他工藝方法實(shí)現(xiàn)加工的零件。
③鑄件材料不受限制,各種合金材料如:碳素鋼、不銹鋼、合金鋼、鋁合金、高溫合金、以及貴重金屬等材料,尤其是難以用鍛造、焊接和切削加工的合金材料。
④生產(chǎn)靈活性好,適應(yīng)性強(qiáng)。可以大批生產(chǎn),也適用于單件或小批生產(chǎn)。
⑤溶模鑄造也有一定的局限性,如:工藝流程繁瑣、生產(chǎn)周期長(zhǎng)。由于其可采用的鑄造工藝手段有限,用于鑄造承壓薄殼閥門鑄件時(shí),其承壓能力不能很高。
鑄造缺陷的分析
的鑄件內(nèi)部都是會(huì)有缺陷的,這些缺陷的存在給鑄件的內(nèi)在質(zhì)量帶來很大的隱患,在生產(chǎn)過程中為這些缺陷進(jìn)行的焊補(bǔ)也會(huì)給生產(chǎn)流程帶來很大的負(fù)擔(dān)。尤其是閥門作為承受壓力、溫度的薄殼鑄件,其內(nèi)部的組織致密性重要。因此,鑄件的內(nèi)部缺陷成為影響鑄件質(zhì)量的決定因素。
閥門鑄件的內(nèi)部缺陷主要有氣孔、夾渣、縮松和裂紋等。
(1)氣孔:氣孔由氣體產(chǎn)生,孔洞表面光滑,產(chǎn)生在鑄件內(nèi)部或近表面,形狀多呈圓形或長(zhǎng)圓形。
生成氣孔的氣體主要來源有:
①金屬中溶解的氮、氫在鑄件凝固的過程中被包容于金屬之中,形成封閉的圓形或橢圓形內(nèi)壁有金屬光澤的氣孔。
②造型材料中的水分或揮發(fā)物質(zhì)都會(huì)因受熱而變成氣體,形成內(nèi)壁為暗褐色的氣孔。
③金屬在澆注過程中,由于流動(dòng)不穩(wěn)定,將空氣卷入而生成氣孔。
氣孔缺陷的防止方法:
①在冶煉方面應(yīng)盡量少用或不用銹蝕的金屬原料,工具和鋼水包要烘烤干燥。
②鋼水澆注要高溫出爐、低溫澆注,鋼水要適當(dāng)鎮(zhèn)靜以利于氣體的上浮。
③澆冒口的工藝設(shè)計(jì)要增大鋼水的壓頭,避免氣體卷入,并設(shè)置人工氣路,合理排氣。
④造型材料要控制含水量、發(fā)氣量,增加透氣性,砂型和砂芯要盡量烘烤干燥。
(2)縮孔(松):它是產(chǎn)生在鑄件內(nèi)部的(尤其是在熱節(jié)部位)呈連貫或不連貫的圓形或不規(guī)則的空洞(腔),內(nèi)表面粗糙,顏色較暗,金屬晶粒粗大,多呈樹枝狀結(jié)晶,聚集在一處或多處,水壓試驗(yàn)時(shí)容易發(fā)生滲漏。
產(chǎn)生縮孔(松)的原因:金屬由液態(tài)凝固為固態(tài)時(shí)發(fā)生體積收縮,此時(shí)如得不到足夠的鋼水補(bǔ)充,則必然產(chǎn)生縮孔。鑄鋼件的縮孔基本是由于對(duì)順序凝固過程控制不當(dāng)而造成的,原因可能有冒口設(shè)置不正確、鋼水澆注溫度過高,金屬收縮量大等。
防止縮孔(松)產(chǎn)生的方法:①科學(xué)的設(shè)計(jì)鑄件的澆注系統(tǒng),使鋼水實(shí)現(xiàn)順序凝固,先凝固的部位應(yīng)有鋼水補(bǔ)充。②正確、合理的設(shè)置冒口、補(bǔ)貼、內(nèi)外冷鐵,確保順序凝固。③在鋼水澆注時(shí),后從冒口處頂注補(bǔ)澆有利于保證鋼水溫度和補(bǔ)縮,減少縮孔的產(chǎn)生。④在澆注速度方面,低速澆注比高速澆注有利于順序凝固。⑸在澆注溫度方面不宜過高,鋼水高溫出爐,經(jīng)后澆注,有利于減少縮孔。
(3)夾砂(渣):夾砂(渣)俗稱砂眼,是在鑄件的內(nèi)部出現(xiàn)不連貫的圓形的或不規(guī)則的孔洞,孔內(nèi)夾雜著型砂或鋼渣,尺寸大小沒有規(guī)律,聚集在一處或多處,往往在上型的部分較多。
產(chǎn)生夾砂(渣)的原因:夾渣是由于鋼水在冶煉或澆注過程中,離散的鋼渣隨著鋼水進(jìn)入鑄件形成的。夾砂是由于造型時(shí)型腔的緊實(shí)度不夠,當(dāng)鋼水澆入型腔時(shí),型砂被鋼水沖起進(jìn)入鑄件內(nèi)部造成的。另外修型、合箱時(shí)不當(dāng),有掉砂現(xiàn)象也是造成夾砂的原因。
防止夾砂(渣)產(chǎn)生的方法:①鋼水冶煉時(shí)要盡量排氣排渣徹底,鋼水出爐后在鋼水包里鎮(zhèn)靜一下,有利于鋼渣的上浮。②鋼水的澆注包盡量不用翻包,而用茶壺包或底注包,以免鋼水上部的渣子順著鋼水進(jìn)入鑄件型腔。③在鋼水澆注時(shí)要采取蓖渣措施,盡量減少鋼渣隨鋼水進(jìn)入型腔。④為了減少夾砂的可能,在造型時(shí)要保證砂型的緊實(shí)度,修型時(shí)注意不要掉砂,合箱前要將型腔吹干凈。
(4)裂紋:鑄件的裂紋大多為熱裂紋,其形狀不規(guī)則,有穿透或不穿透、連續(xù)或斷續(xù),裂紋處的金屬呈暗色或有表面氧化。
產(chǎn)生裂紋的原因:有兩個(gè)方面,即高溫應(yīng)力與液膜變形。
高溫應(yīng)力是鋼水在高溫下收縮變形受阻而形成的應(yīng)力,當(dāng)該應(yīng)力超過了金屬在該溫度下的強(qiáng)度或塑性變形時(shí)便產(chǎn)生了裂紋。液膜變形是鋼水在凝固結(jié)晶過程中晶粒之間產(chǎn)生液膜,隨著凝固結(jié)晶的進(jìn)行,液膜發(fā)生變形,變形量和變形速度超過一定時(shí),便產(chǎn)生了裂紋。熱裂紋產(chǎn)生的溫度范圍約在1200~1450℃左右。
產(chǎn)生裂紋的影響因素:
①鋼中S、P元素是產(chǎn)生裂紋的有害因素,他們和鐵的共晶物了鑄鋼在高溫的強(qiáng)度和塑性,導(dǎo)致裂紋產(chǎn)生。
②鋼中的夾渣和偏析增加了應(yīng)力集中,因而增加了熱裂傾向。
③鋼種的線收縮系數(shù)越大,熱裂的傾向越大。
④鋼種的導(dǎo)熱系數(shù)越大,表面張力越大,高溫機(jī)械性能好,熱裂的傾向越小。
⑤鑄件的結(jié)構(gòu)設(shè)計(jì)工藝性不好,如圓角太小、壁厚懸殊太大、應(yīng)力集中嚴(yán)重,都會(huì)產(chǎn)生裂紋。
⑥砂型的緊實(shí)度太高,型芯的退讓性不良阻礙鑄件收縮會(huì)增加裂紋傾向。
⑦其它如澆冒口排列不當(dāng)、鑄件冷卻速度太快、切割澆冒口及熱處理造成過大應(yīng)力等也都會(huì)影響裂紋的產(chǎn)生。
針對(duì)以上裂紋產(chǎn)生的原因和影響因素,采取對(duì)應(yīng)的措施,就可以減少和避免裂紋缺陷的產(chǎn)生。
綜合以上鑄造缺陷產(chǎn)生原因的分析,查找存在的問題,采取相應(yīng)的改進(jìn)措施,就可以找到解決鑄造缺陷的方法,有利于鑄件質(zhì)量的提高。