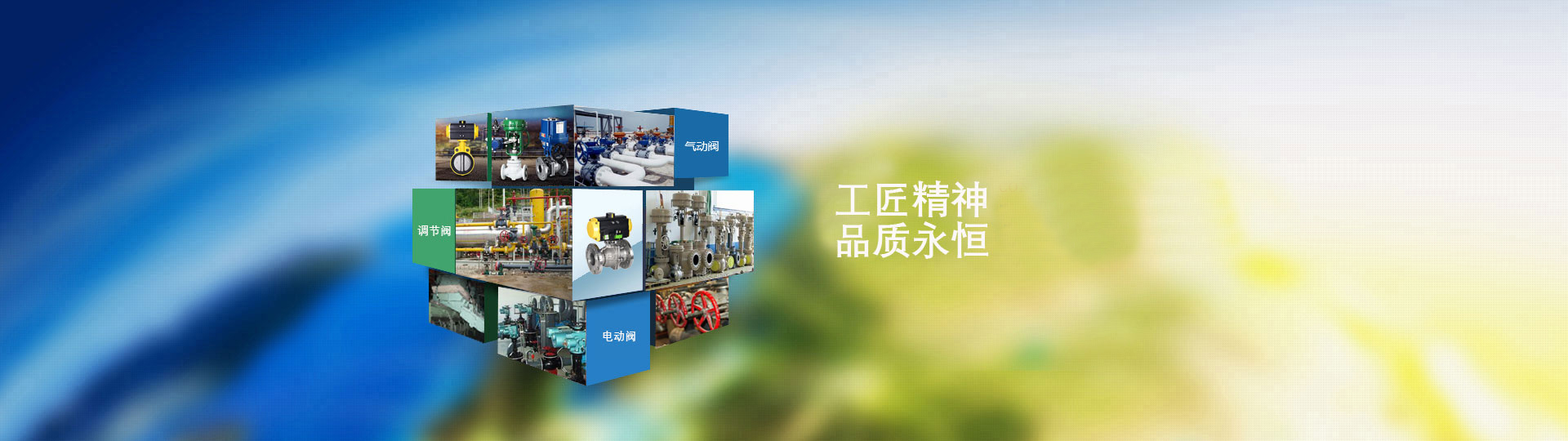
機(jī)械加工基本常識,閥門人必備!更新日期:2021-04-16
(一)基準(zhǔn)
零件都是由若干表面組成,各表面之間有一定的尺寸和相互位置要求。零件表面間的相對位置要求包括兩方面:表面間的距離尺寸精度和相對位置精度(如同軸度、平行度、垂直度和圓跳動等)要求。研究零件表面間的相對位置關(guān)系離不開基準(zhǔn),不明確基準(zhǔn)就無法確定零件表面的位置。基準(zhǔn)就其一般意義來講,就是零件上用以確定其他點、線、面的位置所依據(jù)的點、線、面;鶞(zhǔn)按其作用不同,可分為設(shè)計基準(zhǔn)和工藝基準(zhǔn)兩大類。
1、設(shè)計基準(zhǔn)
在零件圖上用以確定其他點、線、面的基準(zhǔn),稱為設(shè)計基準(zhǔn),就活塞來說,設(shè)計基準(zhǔn)指活塞線和銷孔線。
2、工藝基準(zhǔn)
零件在加工和裝配過程中所使用的基準(zhǔn),稱為工藝基準(zhǔn)。工藝基準(zhǔn)按用途不同,又分為定位基準(zhǔn)、測量基準(zhǔn)和裝配基準(zhǔn)。
(1)定位基準(zhǔn):加工時使工件在機(jī)床或夾具中占據(jù)正確位置所用的基準(zhǔn),稱為定位基準(zhǔn)。按定位元件的不同,常用的有以下兩類:
自動定心定位:如三爪卡盤定位。
定位套定位:將定位元件做成定位套,如止口盤定位
其他有在V形架中定位,在半圓孔中定位等。
(2)測量基準(zhǔn):零件檢驗時,用以測量已加工表面尺寸及位置的基準(zhǔn),稱為測量基準(zhǔn)。
(3)裝配基準(zhǔn):裝配時用以確定零件在部件或產(chǎn)品中位置的基準(zhǔn),稱為裝配基準(zhǔn)。
(二)工件的安裝方式
為了在工件的某一部位上加工出符合規(guī)定技術(shù)要求的表面,在機(jī)械加工前,必須使工件在機(jī)床上相對于工具占據(jù)某一正確的位置。通常把這個過程稱為工件的“定位”。工件定位后,由于在加工中受到切削力、重力等的作用,還應(yīng)采用一定的機(jī)構(gòu)將工件“夾緊”,使其確定的位置保持不變。使工件在機(jī)床上占有正確的位置并將工件夾緊的過程稱為“安裝”。
工件安裝的好壞是機(jī)械加工中的重要問題,它不僅直接影響加工精度、工件安裝的快慢、穩(wěn)定性,還影響生產(chǎn)率的高低。為了保證加工表面與其設(shè)計基準(zhǔn)間的相對位置精度,工件安裝時應(yīng)使加工表面的設(shè)計基準(zhǔn)相對機(jī)床占據(jù)一正確的位置。如精車環(huán)槽工序,為了保證環(huán)槽底徑與裙部軸線的圓跳動的要求,工件安裝時必須使其設(shè)計基準(zhǔn)與機(jī)床主軸的軸心線重合。
在各種不同的機(jī)床上加工零件時,有各種不同的安裝方法。安裝方法可以歸納為直接找正法、劃線找正法和采用夾具安裝法等3種。
(1)直接找正法采用這種方法時,工件在機(jī)床上應(yīng)占有的正確位置,是通過一系列的嘗試而獲得的。具體的方式是將工件直接裝在機(jī)床上后,用百分表或劃針盤上的劃針,以目測法校正工件的正確位置,一邊校驗一邊找正,直符合要求。
直接找正法的定位精度和找正的快慢,取決于找正精度、找正方法、找正工具和工人的技術(shù)水平。它的缺點是花費時間多,生產(chǎn)率低,且要憑經(jīng)驗,對工人技術(shù)的要求高,故僅用于單件、小批量生產(chǎn)中。如硬靠模仿形體的找正就屬于直接找正法。
(2)劃線找正法此法是在機(jī)床上用劃針按毛坯或半成品上所劃的線來找正工件,使其獲得正確位置的一種方法。顯而易見,此法要多一道劃線工序。劃出的線本身有一定寬度,在劃線時又有劃線誤差,校正工件位置時還有觀察誤差,因此該法多用于生產(chǎn)批量較小,毛坯精度較低,以及大型工件等不宜使用夾具的粗加工中。如二沖程產(chǎn)品銷釘孔位置的確定就是使 用分度頭的劃線法找正。
(3)采用夾具安裝法:用于裝夾工件,使之占有正確位置的工藝裝備稱為機(jī)床夾具。夾具是機(jī)床的一種附加裝置,它在機(jī)床上相對刀具的位置在工件未安裝前已預(yù)先調(diào)整好,所以在加工一批工件時不必再逐個找正定位,就能保證加工的技術(shù)要求,既省工又省事,是的定位方法,在成批和大量生產(chǎn)中廣泛應(yīng)用。我們現(xiàn)在的活塞加工就是使用的夾具安裝法。
1)工件定位后,使其在加工過程中保持定位位置不變的,稱為夾緊。夾具中使工件在加工過程中保持定位位置不變的裝置,叫夾緊裝置。
2)夾緊裝置應(yīng)符合以下幾點要求:夾緊時,不應(yīng)破壞工件的定位;夾緊后,應(yīng)保證工件在加工過程中的位置不發(fā)生變化,夾緊準(zhǔn)確、可靠;夾緊動作迅速,方便、省力;結(jié)構(gòu)簡單,制造容易。
3)夾緊時的注意事項:夾緊力大小要適當(dāng),過大會造成工件變形,過小會使工件在加工過程中產(chǎn)生位移,破壞工件定位。
(三)金屬切削基本知識
1、車削運動及形成的表面
車削運動:在切削過程中,為了切除多余的金屬,必需使工件和刀具作相對的切削運動,在車床上用車刀切除工件上多余金屬的運動稱為車削運動,可分為主運動和進(jìn)給運動。
主運動:直接切除工件上的切削層,使之轉(zhuǎn)變?yōu)榍行迹瑥亩纬晒ぜ卤砻娴倪\動,稱主運動。切削時,工件的旋轉(zhuǎn)運動是主運動。通常,主運動的速度較高,消耗的切削功率較大。
進(jìn)給運動:使新的切削層不斷投入切削的運動,進(jìn)給運動是沿著所要形成的工件表面的運動,可以是連續(xù)運動,也可以是間歇運動。如臥式車床上車刀的運動時連續(xù)運動,牛頭刨床上工件的進(jìn)給運動為間歇運動。
工件上形成的表面:在切削過程中,在工件上形成已加工表面、加工表面和待加工表面。已加工表面指已經(jīng)車去多余金屬而形成的新表面。待加工表面指即將被切去金屬層的表面。加工表面指車刀切削刃正在車削的表面。
2、切削用量三要素是指切削深度、進(jìn)給量和切削速度。
(1)切削深度:ap=(dw-dm)/2(mm) dw=未加工工件直徑 dm=已加工工件直徑,切削深度也就是我們通常所說的吃刀量。
切削深度的選擇:切削深度αp應(yīng)根據(jù)加工余量確定。粗加工時,除留下精加工的余量外,應(yīng)盡可能一次走刀切除全部粗加工余量。這不僅能在保證一定耐用度的前提下使切削深度、進(jìn)給量?、切削速度V的乘積大,而且可以減少走刀次數(shù)。在加工余量過大或工藝系統(tǒng)剛度不足或刀片強(qiáng)度不足等情況下,應(yīng)分成兩次以上走刀。這時,應(yīng)將一次走刀的切削深度取大些,可占全部余量的2/3~3/4;而使***次走刀的切削深度小些,以使精加工工序獲得較小的表面粗糙度參數(shù)值及較高的加工精度。
切削零件表層有硬皮的鑄、鍛件或不銹鋼等冷硬較嚴(yán)重的材料時,應(yīng)使切削深度超過硬度或冷硬層,以避免切削刃在硬皮或冷硬層上切削。
(2)進(jìn)給量的選擇:工件或工具每旋轉(zhuǎn)一周或往復(fù)一次,工件與工具在進(jìn)給運動方向上的相對位移,單位為mm。切削深度選定之后,應(yīng)進(jìn)一步盡量選擇較大的進(jìn)給量。進(jìn)給量其合理數(shù)值的選擇應(yīng)保證機(jī)床、刀具不致因切削力太大而損壞,切削力所造成的工件撓度不致超出工件精度允許的數(shù)值,表面粗糙度參數(shù)值不致太大。粗加工時,限制進(jìn)給量的主要是切削力,半精加工和精加工時,限制進(jìn)給量的主要是表面粗糙度。
(3)切削速度的選擇:在進(jìn)行切削加工時,工具切削刃上的某一點相對于待加工表面在主運動方向上的瞬時速度, 單位為m/min,。當(dāng)切削深度αp與進(jìn)給量?選定后,在些基礎(chǔ)上再選大的切削速度,切削加工的發(fā)展方向是高速切削加工。
(四)粗糙度機(jī)械學(xué)概念
在機(jī)械學(xué)中,粗糙度指加工表面上具有的較小間距和峰谷所組成的微觀幾何形狀特性。它是互換性研究的問題之一。表面粗糙度一般是由所采用的加工方法和其他因素所形成的,例如加工過程中刀具與零件表面間的摩擦、切屑分離時表面層金屬的塑性變形以及工藝系統(tǒng)中的高頻振動等。由于加工方法和工件材料的不同,被加工表面留下痕跡的深淺、疏密、形狀和紋理都有差別。表面粗糙度與機(jī)械零件的配合性質(zhì)、耐磨性、疲勞強(qiáng)度、接觸剛度、振動和噪聲等有密切關(guān)系,對機(jī)械產(chǎn)品的使用和可靠性有重要影響。
粗糙度表示方式
零件表面經(jīng)過加工后,看起來很光滑,經(jīng)放大觀察卻凹凸不平。表面精糙度,是指加工后的零件表面上具有的較小間距和微小峰谷所組成的微觀幾何形狀特征,一般是由所采取的加工方法和(或)其他因素形成的。零件表面的功用不同,所需的表面粗糙度參數(shù)值也不一樣。零件圖上要標(biāo)注表面粗糙度代(符)號,用以說明該表面完工后須達(dá)到的表面特性。表
面粗糙度高度參數(shù)有3種:
1、輪廓算術(shù)平均偏差Ra
在取樣長度內(nèi),沿測量方向(Y方向)的輪廓線上的點與基準(zhǔn)線之間距離值的算術(shù)平均值。
2、微觀不平度十點高度Rz
指在取樣長度內(nèi)5個大輪廓峰高的平均值和5個大輪廓谷深的平均值之和。
3、輪廓大高度Ry
在取樣長度內(nèi),輪廓高峰頂線和低谷底線之間的距離。
目前,一般機(jī)械制造工業(yè)中主要選用Ra.
4.粗糙度表示方法
5.粗糙度對零件進(jìn)行性能的影響
工件加工后的表面質(zhì)量直接影響被加工件的物理、化學(xué)及力學(xué)性能,產(chǎn)品的工作性能、可靠性、在很大程度上取決于主要零件的表面質(zhì)量。一般而言,重要或關(guān)鍵零件的表面質(zhì)量要求都比普通零件要高,這是因為表面質(zhì)量好的零件會在很大程度上提高其耐磨性、耐蝕性和抗疲勞破損能力。
6、切削液
(1)切削液的作用
冷卻作用:切削熱能帶走大量的切削熱,改善散熱條件,刀具和工件的溫度,從而延長了刀具的使用,可防止工件因熱變形而產(chǎn)生的尺寸誤差。
潤滑作用:切削液能滲透到工件與刀具之間,使切屑與刀具之間的微小間隙中形成一層薄薄的吸附膜,減小了摩擦系數(shù),因此可減少刀具切屑與工件之間的摩擦,使切削 力和切削熱,減少刀具的磨損并能提高工件的表面質(zhì)量,對于精加工,潤滑尤其重要。
清洗作用:清洗過程中產(chǎn)生的微小的切屑易粘附在工件和刀具上,尤其是鉆深孔和絞孔時,切屑容易堵塞在容屑槽中,影響工件的表面粗糙度和刀具的使用。使用切削液能將切屑迅速沖走,是切削順利進(jìn)行。
(2)種類:常用切削液有兩大類
乳化液:主要起冷卻作用,乳化液是把乳化油用15~20倍的水稀釋而成,這類切削液的比熱大,粘度小,流動性好,可以吸收大量的熱,使用這類切削液主要是為了冷卻刀具和工件,提高刀具,減少熱變形。乳化液中含水較多,潤滑和防銹功能較差。
切削油:切削油的主要成分是礦物油,這類切削液的比熱較小,粘度較大,流動性差,主要起潤滑作用,常用的是粘度較低的礦物油,如機(jī)油、輕柴油、煤油等。
零件都是由若干表面組成,各表面之間有一定的尺寸和相互位置要求。零件表面間的相對位置要求包括兩方面:表面間的距離尺寸精度和相對位置精度(如同軸度、平行度、垂直度和圓跳動等)要求。研究零件表面間的相對位置關(guān)系離不開基準(zhǔn),不明確基準(zhǔn)就無法確定零件表面的位置。基準(zhǔn)就其一般意義來講,就是零件上用以確定其他點、線、面的位置所依據(jù)的點、線、面;鶞(zhǔn)按其作用不同,可分為設(shè)計基準(zhǔn)和工藝基準(zhǔn)兩大類。
1、設(shè)計基準(zhǔn)
在零件圖上用以確定其他點、線、面的基準(zhǔn),稱為設(shè)計基準(zhǔn),就活塞來說,設(shè)計基準(zhǔn)指活塞線和銷孔線。
2、工藝基準(zhǔn)
零件在加工和裝配過程中所使用的基準(zhǔn),稱為工藝基準(zhǔn)。工藝基準(zhǔn)按用途不同,又分為定位基準(zhǔn)、測量基準(zhǔn)和裝配基準(zhǔn)。
(1)定位基準(zhǔn):加工時使工件在機(jī)床或夾具中占據(jù)正確位置所用的基準(zhǔn),稱為定位基準(zhǔn)。按定位元件的不同,常用的有以下兩類:
自動定心定位:如三爪卡盤定位。
定位套定位:將定位元件做成定位套,如止口盤定位
其他有在V形架中定位,在半圓孔中定位等。
(2)測量基準(zhǔn):零件檢驗時,用以測量已加工表面尺寸及位置的基準(zhǔn),稱為測量基準(zhǔn)。
(3)裝配基準(zhǔn):裝配時用以確定零件在部件或產(chǎn)品中位置的基準(zhǔn),稱為裝配基準(zhǔn)。
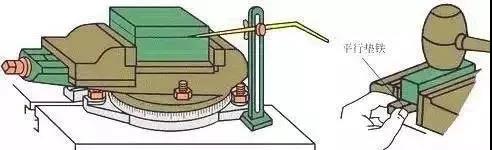
(二)工件的安裝方式
為了在工件的某一部位上加工出符合規(guī)定技術(shù)要求的表面,在機(jī)械加工前,必須使工件在機(jī)床上相對于工具占據(jù)某一正確的位置。通常把這個過程稱為工件的“定位”。工件定位后,由于在加工中受到切削力、重力等的作用,還應(yīng)采用一定的機(jī)構(gòu)將工件“夾緊”,使其確定的位置保持不變。使工件在機(jī)床上占有正確的位置并將工件夾緊的過程稱為“安裝”。
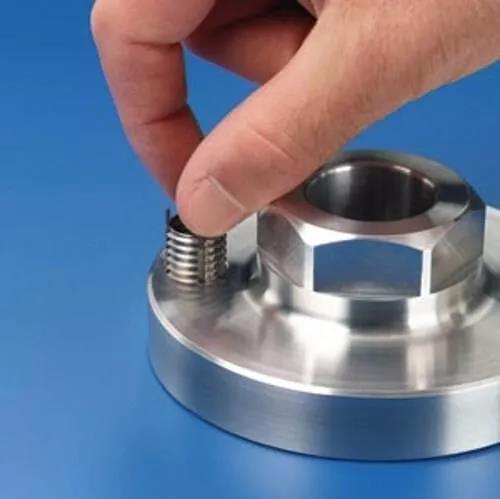
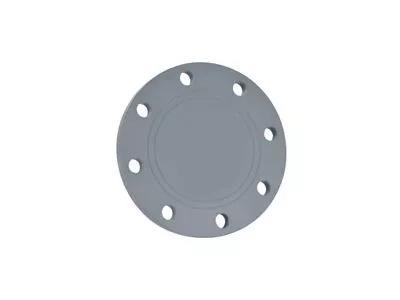
(1)直接找正法采用這種方法時,工件在機(jī)床上應(yīng)占有的正確位置,是通過一系列的嘗試而獲得的。具體的方式是將工件直接裝在機(jī)床上后,用百分表或劃針盤上的劃針,以目測法校正工件的正確位置,一邊校驗一邊找正,直符合要求。
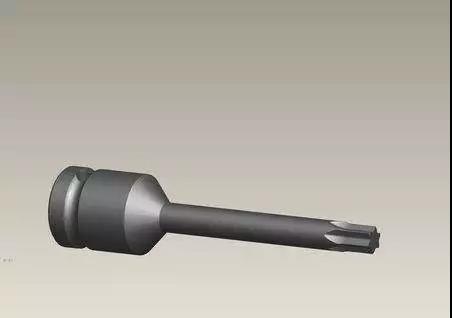
(2)劃線找正法此法是在機(jī)床上用劃針按毛坯或半成品上所劃的線來找正工件,使其獲得正確位置的一種方法。顯而易見,此法要多一道劃線工序。劃出的線本身有一定寬度,在劃線時又有劃線誤差,校正工件位置時還有觀察誤差,因此該法多用于生產(chǎn)批量較小,毛坯精度較低,以及大型工件等不宜使用夾具的粗加工中。如二沖程產(chǎn)品銷釘孔位置的確定就是使 用分度頭的劃線法找正。
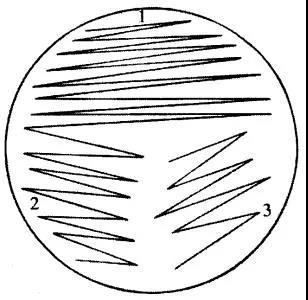
1)工件定位后,使其在加工過程中保持定位位置不變的,稱為夾緊。夾具中使工件在加工過程中保持定位位置不變的裝置,叫夾緊裝置。
2)夾緊裝置應(yīng)符合以下幾點要求:夾緊時,不應(yīng)破壞工件的定位;夾緊后,應(yīng)保證工件在加工過程中的位置不發(fā)生變化,夾緊準(zhǔn)確、可靠;夾緊動作迅速,方便、省力;結(jié)構(gòu)簡單,制造容易。
3)夾緊時的注意事項:夾緊力大小要適當(dāng),過大會造成工件變形,過小會使工件在加工過程中產(chǎn)生位移,破壞工件定位。
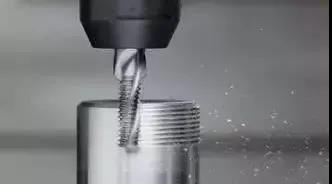
(三)金屬切削基本知識
1、車削運動及形成的表面
車削運動:在切削過程中,為了切除多余的金屬,必需使工件和刀具作相對的切削運動,在車床上用車刀切除工件上多余金屬的運動稱為車削運動,可分為主運動和進(jìn)給運動。
主運動:直接切除工件上的切削層,使之轉(zhuǎn)變?yōu)榍行迹瑥亩纬晒ぜ卤砻娴倪\動,稱主運動。切削時,工件的旋轉(zhuǎn)運動是主運動。通常,主運動的速度較高,消耗的切削功率較大。
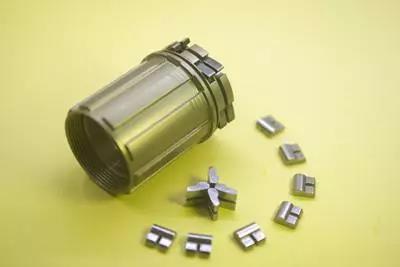
工件上形成的表面:在切削過程中,在工件上形成已加工表面、加工表面和待加工表面。已加工表面指已經(jīng)車去多余金屬而形成的新表面。待加工表面指即將被切去金屬層的表面。加工表面指車刀切削刃正在車削的表面。
2、切削用量三要素是指切削深度、進(jìn)給量和切削速度。
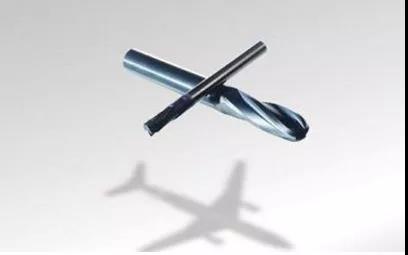
切削深度的選擇:切削深度αp應(yīng)根據(jù)加工余量確定。粗加工時,除留下精加工的余量外,應(yīng)盡可能一次走刀切除全部粗加工余量。這不僅能在保證一定耐用度的前提下使切削深度、進(jìn)給量?、切削速度V的乘積大,而且可以減少走刀次數(shù)。在加工余量過大或工藝系統(tǒng)剛度不足或刀片強(qiáng)度不足等情況下,應(yīng)分成兩次以上走刀。這時,應(yīng)將一次走刀的切削深度取大些,可占全部余量的2/3~3/4;而使***次走刀的切削深度小些,以使精加工工序獲得較小的表面粗糙度參數(shù)值及較高的加工精度。

(2)進(jìn)給量的選擇:工件或工具每旋轉(zhuǎn)一周或往復(fù)一次,工件與工具在進(jìn)給運動方向上的相對位移,單位為mm。切削深度選定之后,應(yīng)進(jìn)一步盡量選擇較大的進(jìn)給量。進(jìn)給量其合理數(shù)值的選擇應(yīng)保證機(jī)床、刀具不致因切削力太大而損壞,切削力所造成的工件撓度不致超出工件精度允許的數(shù)值,表面粗糙度參數(shù)值不致太大。粗加工時,限制進(jìn)給量的主要是切削力,半精加工和精加工時,限制進(jìn)給量的主要是表面粗糙度。
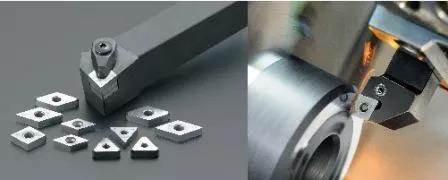
(3)切削速度的選擇:在進(jìn)行切削加工時,工具切削刃上的某一點相對于待加工表面在主運動方向上的瞬時速度, 單位為m/min,。當(dāng)切削深度αp與進(jìn)給量?選定后,在些基礎(chǔ)上再選大的切削速度,切削加工的發(fā)展方向是高速切削加工。
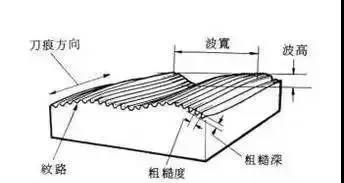
(四)粗糙度機(jī)械學(xué)概念
在機(jī)械學(xué)中,粗糙度指加工表面上具有的較小間距和峰谷所組成的微觀幾何形狀特性。它是互換性研究的問題之一。表面粗糙度一般是由所采用的加工方法和其他因素所形成的,例如加工過程中刀具與零件表面間的摩擦、切屑分離時表面層金屬的塑性變形以及工藝系統(tǒng)中的高頻振動等。由于加工方法和工件材料的不同,被加工表面留下痕跡的深淺、疏密、形狀和紋理都有差別。表面粗糙度與機(jī)械零件的配合性質(zhì)、耐磨性、疲勞強(qiáng)度、接觸剛度、振動和噪聲等有密切關(guān)系,對機(jī)械產(chǎn)品的使用和可靠性有重要影響。
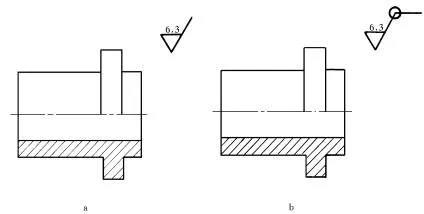
粗糙度表示方式
零件表面經(jīng)過加工后,看起來很光滑,經(jīng)放大觀察卻凹凸不平。表面精糙度,是指加工后的零件表面上具有的較小間距和微小峰谷所組成的微觀幾何形狀特征,一般是由所采取的加工方法和(或)其他因素形成的。零件表面的功用不同,所需的表面粗糙度參數(shù)值也不一樣。零件圖上要標(biāo)注表面粗糙度代(符)號,用以說明該表面完工后須達(dá)到的表面特性。表
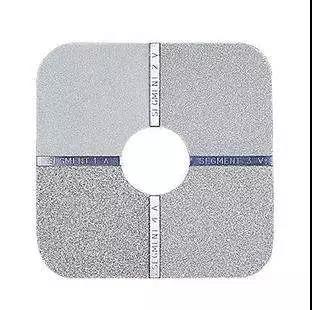
1、輪廓算術(shù)平均偏差Ra
在取樣長度內(nèi),沿測量方向(Y方向)的輪廓線上的點與基準(zhǔn)線之間距離值的算術(shù)平均值。
2、微觀不平度十點高度Rz
指在取樣長度內(nèi)5個大輪廓峰高的平均值和5個大輪廓谷深的平均值之和。
3、輪廓大高度Ry
在取樣長度內(nèi),輪廓高峰頂線和低谷底線之間的距離。
目前,一般機(jī)械制造工業(yè)中主要選用Ra.
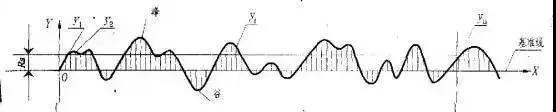
4.粗糙度表示方法
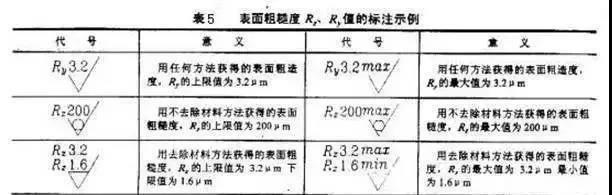
5.粗糙度對零件進(jìn)行性能的影響
工件加工后的表面質(zhì)量直接影響被加工件的物理、化學(xué)及力學(xué)性能,產(chǎn)品的工作性能、可靠性、在很大程度上取決于主要零件的表面質(zhì)量。一般而言,重要或關(guān)鍵零件的表面質(zhì)量要求都比普通零件要高,這是因為表面質(zhì)量好的零件會在很大程度上提高其耐磨性、耐蝕性和抗疲勞破損能力。
6、切削液
(1)切削液的作用
冷卻作用:切削熱能帶走大量的切削熱,改善散熱條件,刀具和工件的溫度,從而延長了刀具的使用,可防止工件因熱變形而產(chǎn)生的尺寸誤差。
潤滑作用:切削液能滲透到工件與刀具之間,使切屑與刀具之間的微小間隙中形成一層薄薄的吸附膜,減小了摩擦系數(shù),因此可減少刀具切屑與工件之間的摩擦,使切削 力和切削熱,減少刀具的磨損并能提高工件的表面質(zhì)量,對于精加工,潤滑尤其重要。
清洗作用:清洗過程中產(chǎn)生的微小的切屑易粘附在工件和刀具上,尤其是鉆深孔和絞孔時,切屑容易堵塞在容屑槽中,影響工件的表面粗糙度和刀具的使用。使用切削液能將切屑迅速沖走,是切削順利進(jìn)行。
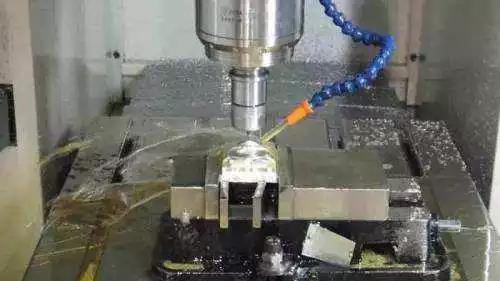
乳化液:主要起冷卻作用,乳化液是把乳化油用15~20倍的水稀釋而成,這類切削液的比熱大,粘度小,流動性好,可以吸收大量的熱,使用這類切削液主要是為了冷卻刀具和工件,提高刀具,減少熱變形。乳化液中含水較多,潤滑和防銹功能較差。
切削油:切削油的主要成分是礦物油,這類切削液的比熱較小,粘度較大,流動性差,主要起潤滑作用,常用的是粘度較低的礦物油,如機(jī)油、輕柴油、煤油等。